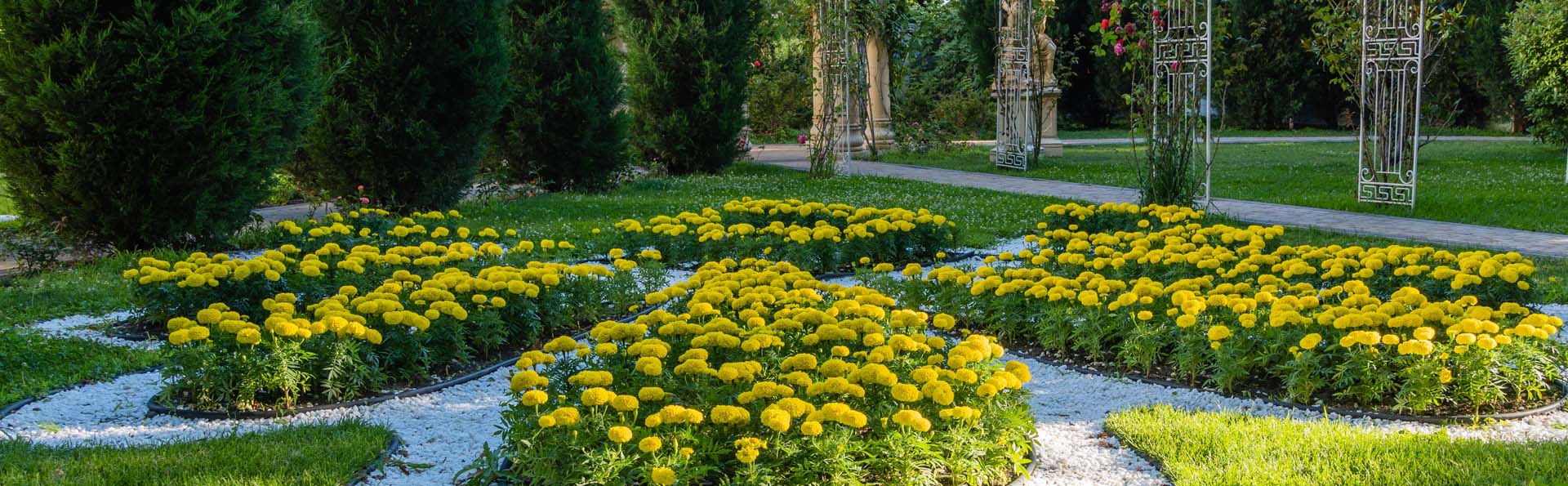
Professional Maintenance of Commercial Mosquito Misting Systems
Professional Maintenance: Key to System Performance
Any commercial-grade mosquito misting system requires regular professional maintenance to ensure its efficiency, effectiveness and longevity. A-Niks maintains all the mosquito misting systems we install to the highest professional standards.
The following is a list of the typical steps involved in our maintenance process, along with explanations for each step:
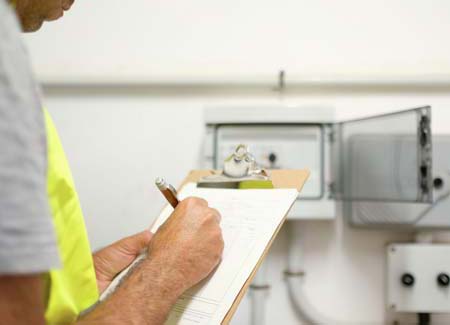
Cleaning: A-Niks technicians clean the misting nozzles, filters and tubing to ensure optimal performance. This involves removing debris such as dirt, leaves, or insect nests, which can clog the nozzles and reduce the mosquito misting system’s effectiveness. Filters must be cleaned or replaced, depending on their condition. We note down any need for replacement.
Nozzle replacement or repair: Worn or damaged nozzles impact a mosquito misting system performance and need to be replaced or repaired. As part of our professional maintenance services, A-Niks technicians replace any malfunctioning nozzles (with your consent) or perform necessary repairs to restore optimal spray patterns and coverage.
Checking and refilling insecticide reservoir: Our technicians inspect the insecticide reservoir for leaks or damage, and refill it with our recommended environmentally friendly insecticide solution. Professional maintenance must ensure that the correct concentration is used to maintain effectiveness and comply with Florida regulations.
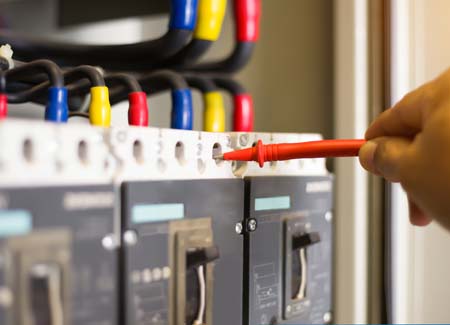
Pressure testing and adjustment: The functional pressure of a mosquito misting system needs to be tested and adjusted to maintain optimal performance. Incorrect pressure levels cause uneven spray coverage or inadequate insecticide delivery. Our technicians ensure that the pressure is within the recommended range for your specific mosquito misting system.
Inspecting and replacing tubing and fittings: A-Niks technicians inspect all tubing and fittings for signs of wear or damage, such as cracks or leaks. Damaged or worn tubing and fittings must be replaced to prevent leaks and maintain optimal system performance.
Lubrication and maintenance of pumps and motors: Our technicians inspect pumps and motors for wear and properly lubrication to ensure smooth operation. Any necessary repairs or replacements are performed to maintain optimal performance and prevent system failure.
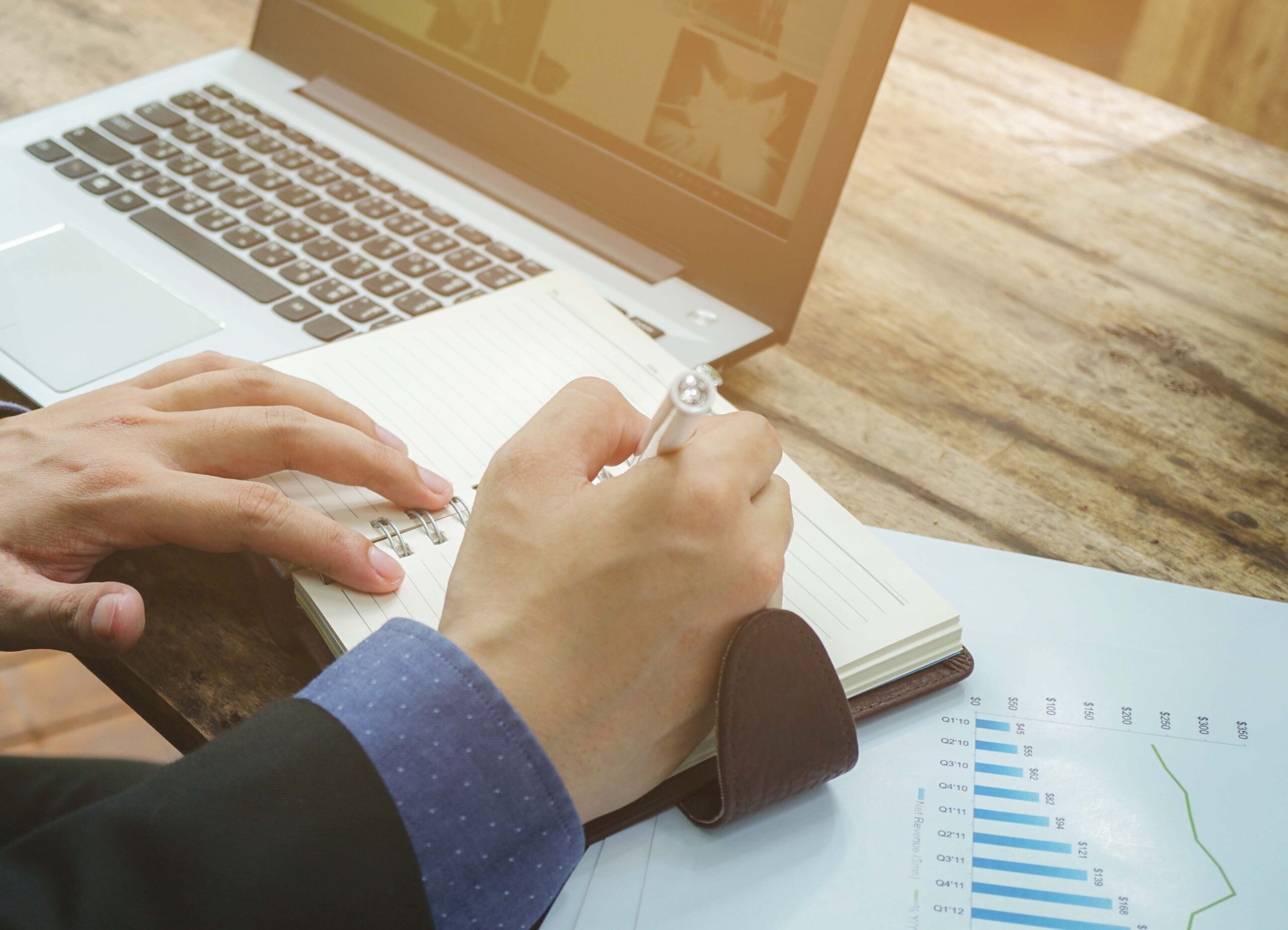
Record keeping and reporting: Lastly, A-Niks technicians document the professional maintenance steps performed, noting down any repairs, replacements, or adjustments carried out. The maintenance record helps track the system’s history and assists in identifying potential issues or repeat repairs that would call for attention in the future.
By following these steps, A-Nicks professional technicians keep the efficiency and effectiveness of the commercial-grade mosquito misting systems we install, ensuring that your system continues to provide reliable mosquito control over your property or facility.